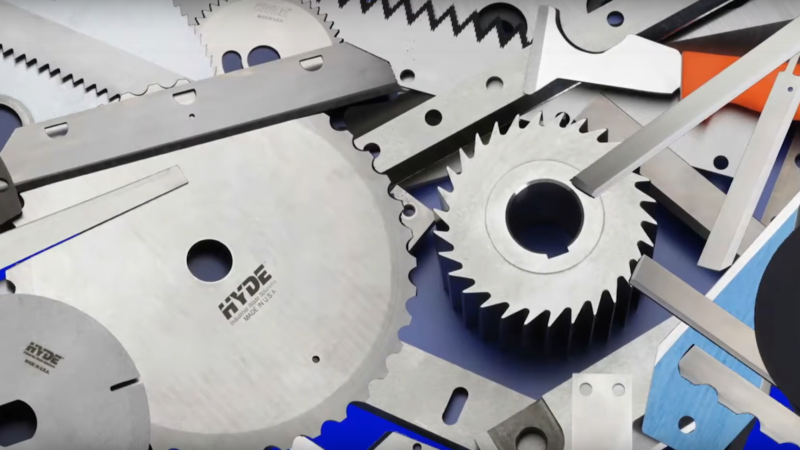
While mechanical blade dicing san jose methods look gentle at the macro level, they can be quite damaging to delicate MEMS devices. The dicing blade is typically bathed in significant amounts of water coolant that can cause vibration and particles to impact the die. DI water typically has a pH of about 7, which can lead to Al corrosion. Narrowing the dicing street would reduce the risk but is challenging due to the structures in the streets themselves.
Reduced Waste
Traditional blade dicing san jose involves placing wafers or other substrates inside of frames and positioning them on a diamond blade that is rotated at between 15,000 and 30,000 rpm. While the blade is cutting. Water or another coolant sprays along its path to help control temperature and prevent silicon residues/particles from contaminating the wafers and/or bonding pads.
This process is not without its challenges, however. As the kerf width (the area cut by the blade) increases, a number of problems can arise, including contamination, wafer chipping, cracks and microcracks, subsurface damage, nonlinearity, and inconsistent cuts. Several interventions have been proposed to improve the quality of dicing results. These include changing the chemistry of the dicing solution, optimizing the cutting parameters, and modifying the dicing blade morphology. In addition, the use of laser dressing has shown promising results for reducing chipping and other defects.
Term of Chemistry
In terms of chemistry, it is necessary to have an effective matrix for binding the diamond abrasive grains to provide excellent abrasion performance. Metal dicing blades that are fabricated using SPS have been shown to an efficient solution because they have low sintering temperatures. Yielding a well-merged diamond abrasive compound matrix.
In a recent study, researchers tested a range of dicing solutions with varying pH levels (ranging from 1:0 to 1:10000) on various materials such as silicon, sintering grade silicon carbide and sintered silicon carbide, sapphire, quartz glass, and dielectric substrates. They found that the optimal pH value was about 5.0 because it afforded low Ni etch rates, long blade life, and moderate CuOx etch rates for cleaning copper bond pads.
Reduced Energy Consumption
Dicing is the process of cutting wafers into smaller sections to form microelectromechanical devices. This includes things like micro-electromechanical systems (MEMSs), infrared filters, integrated circuitry (IC) and more. Traditional blade dicing San Jose involves positioning the wafers in an adhesive film inside a metal frame before slicing them with a diamond blade rotating between 15,000 and 30,000 RPM. As it slices, the blade sprays water or another cooling agent along the edges of the wafer to control temperature and keep dust particles from contaminating the device.
While the dicing process produces good yields, there are some issues with corrosion from the dicing solution and vibration that can cause some devices to fail. One issue is that the dicing solution used during the process is typically deionized water which can cause aluminum (Al) corrosion. To mitigate this, the dicing solution often contains chelating agents to help prevent Al corrosion.
The help of limited amount of time
It also helps to limit the amount of time that the dicing process runs for. This is because the dicing blade will wear down faster when it is running for longer periods of time. One way to extend the life of a diamond dicing blade is to use continuous laser dressing. This will help to remove the excess bonding material and expose sharp diamond abrasive grits for a higher-quality cut. The resulting blade will last longer and reduce the number of times it needs to replaced.
Reduced Chemical Consumption
Blade dicing San Jose cuts through materials to remove substrates from the wafer. The resulting fragments and debris need to disposed of. Traditional blade dicing san jose relies on a mixture of acetone, isopropyl alcohol, and water to flush the debris and fragments from the wafer. This process uses more than a gallon of solvents per wafer, which can have negative environmental impacts. A newer method, plasma dicing, offers better results with a less toxic chemical mixture.
A dicing solution is often used during a blade cut for lubrication, cooling, and particle removal. DI (Deionized) water is the most commonly used dicing solution. However, this can cause Al (Aluminum) corrosion due to the pH of the solution which is about 7. CO2 can injected into the dicing solution to lower its pH to 4-4.5 and reduce the corrosion.
Contaminant
Another contaminant that can reduced is the use of solvents such as acetone, isopropyl, and water to flush the debris from the blade. These solvents also can have a negative impact on the environment and need to disposed of. Blade dicing vibrates the MEMS devices with both the cutting motion and the water contact.
This can cause damage, especially to the fragile dies in compound semiconductors such as GaAs (Gallium Arsenide). To limit this impact on the devices, limiting top and backside chip-out and using laser ablation dicing where possible is a good choice.
Reduced Noise
Traditional blade dicing requires mounting wafers onto an adhesive film inside a metal frame before positioning the frame and wafer on a chuck. A diamond blade then slices the wafer into dies. Water or another cooling agent sprays along the cutting lines to control temperature and prevent dust particles from contaminating the wafer. This process is time-consuming and creates significant noise due to the spinning saw and the high rpm of the blade.
Dicing solutions contain a concentration of organic acids or salts to improve lubrication and extend blade life. As well as surfactants that reduce kerf loss by removing residues from the surfaces of the wafer and dicing blade. These compounds also provide protection against etch-back. The concentration of these compounds can range from 0.001 to 30 wt % (by weight) and may adjusted as needed.
Generate Vibrations
The dicing blade can generate vibrations that damage the surface of the device and create thermal stress in the die. This stress can reduced by covering the wafer with protective tape and limiting the amount of water pressure sprayed on the device during the cutting process. In addition, flooding instead of spraying can help limit the damage caused by the vibration.
Plasma dicing is a promising technology for non-contact etching of semiconductor devices. However, it is still dependent on masking the scribes and removing non-etchable materials such as metal from the streets. This can make it difficult to use in applications where a lot of silicon must exposed or in cases when the backside of the wafer needs to be cleaned.
Thanks for visiting Top magazine