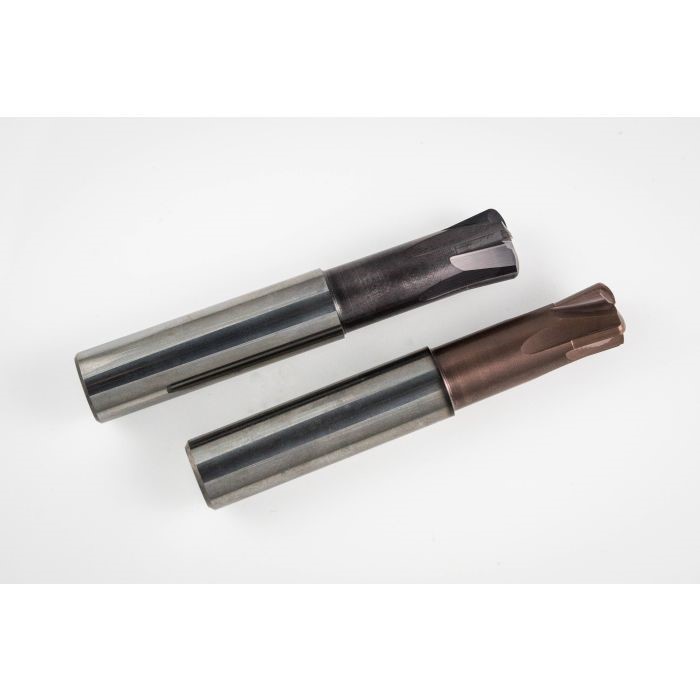
In the intricate world of metalworking, precision and efficiency are paramount. Achieving the perfect cut, smooth surface finish, and extending the lifespan of your tools can hinge on one critical aspect: speed and feed rates.
In this article, we will explore the pivotal role of speed and feed rates when using aluminum carbide burrs.
Speed and Feed Rates Defined
Speed and feed rates are fundamental concepts in the world of machining and metalworking. Speed refers to the rotational speed of the tool, usually measured in revolutions per minute (RPM), while feed rate relates to the linear speed at which the tool advances through the workpiece, often expressed in inches per minute (IPM) or millimeters per minute (mm/min). These rates determine the pace and quality of the cutting process.
The Relationship Between Speed and Feed Rates
Speed and feed rates are interconnected; changing one directly affects the other and the overall machining process. By adjusting speed and feed rates, you can control chip load, tool life, surface finish, and heat generation.
Factors Influencing Speed and Feed Rates
Selecting the appropriate speed and feed rates involves considering several factors, including the type and hardness of the material, the shape and size of the burr, the condition of the tool, and the machining environment. These factors influence the efficiency and quality of the machining process.
Calculating Optimal Speed and Feed Rates
To achieve the best results with aluminum carbide burr set, machinists can calculate optimal speed and feed rates based on material properties and specific burr characteristics. Formulas and methods can guide these calculations, ensuring precision and efficiency.
Importance of Proper Speed and Feed Rates
Using the correct speed and feed rates is essential for several reasons:
- Precise Cuts and Surface Finishes: Proper rates result in accurate cuts and smooth surface finishes.
- Tool Wear Reduction: Correct rates minimize tool wear, extending the lifespan of aluminum carbide burrs.
- Heat Generation Control: Adequate rates help manage heat generation, preventing workpiece damage.
- Overall Efficiency: Optimized rates enhance overall machining efficiency, saving time and resources.
Speed and Feed Rate Guidelines for Common Materials
Different materials require specific speed and feed rate settings. Guidelines for materials like aluminum, steel, and brass can assist machinists in achieving optimal results with aluminum carbide burrs.
Monitoring and Adjusting Speed and Feed Rates
Ongoing monitoring during the machining process is essential. Detecting issues such as chatter or excessive tool wear allows for timely adjustments to speed and feed rates, ensuring the best possible outcomes.
See more information at odidea.net
Troubleshooting Common Speed and Feed Rate Issues
Identifying and addressing common problems that arise from incorrect speed and feed rates is crucial. Troubleshooting tips and solutions can help machinists overcome challenges.
Final Thoughts:
Speed and feed rates are the heartbeats of successful metalworking with aluminum carbide burrs. Precision, efficiency, and quality hinge on these critical parameters. By understanding and optimizing speed and feed rates, metalworkers can unlock the full potential of their aluminum carbide burrs set, achieving exceptional results in their projects. Make sure to visit the Burrs4less website to buy high-quality carbide burrs for precision and excellence in every project.