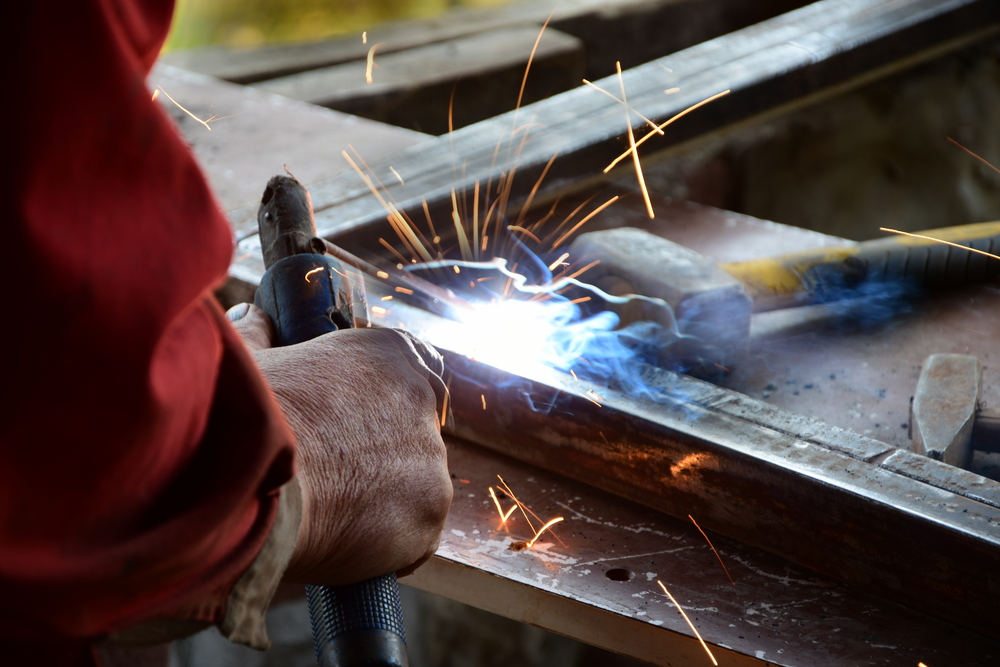
Sheet Metal Fabricators are the unsung heroes in our modern society, often overlooked yet integral to numerous sectors like automotive, aerospace, construction, and electronics. But what do these experts do exactly? What intricate processes do they master and tools do they wield to transform a simple sheet of metal into a functional, often vital, component? This article aims to demystify the world of sheet metal fabricators, offering a deep dive into their role, the fabrication process, materials used, and much more.
What is Sheet Metal Fabrication?
Sheet Metal Fabrication is a multidisciplinary process that involves shaping, bending, cutting, and assembling metal sheets into various products. From your car’s bodywork to an airplane’s wing, these products are everywhere, underscoring the importance of this industrial art form.
The Role of Sheet Metal Fabricators
Sheet Metal Fabricators are the skilled artisans behind this process. Their expertise spans interpreting blueprints, selecting appropriate materials, cutting and shaping them, and finally assembling the final product. Their work is a testament to precision, attention to detail, and an understanding of the material’s physical properties.
Key Steps in the Sheet Metal Fabrication Process
The fabrication process typically involves cutting, forming, and assembling. Cutting involves slicing the sheet metal into desired shapes using tools like lasers, plasma torches, or water jets. Forming bends the cut pieces using press brakes or similar machinery. Finally, the assembly involves joining these pieces together using techniques like welding, riveting, or using adhesives.
Commonly Used Sheet Metal Materials
The choice of material depends on the project requirements. Common materials include steel, aluminum, copper, and brass. Each material has its strengths and weaknesses, and understanding these is crucial to the fabrication process.
Essential Tools for Sheet Metal Fabrication
Sheet Metal Fabrication tools range from hand-held tools like hammers and snips to high-tech machinery like Computer Numerical Control (CNC) machines. These tools enable the precise shaping, cutting, and assembly of metal sheets.
Custom vs. Industrial Sheet Metal Fabrication
Custom fabrication involves creating unique components for specific applications, while industrial fabrication involves mass production of components. Both require a high level of expertise but differ in their approach and scale.
The Importance of Sheet Metal Design
Designing for sheet metal fabrication involves balancing aesthetics, functionality, and manufacturability. It’s a collaborative process involving fabricators, designers, and engineers to ensure the final product meets all its objectives without compromising on quality.
Sheet Metal Finishing Techniques
Finishing techniques like sanding, painting, or coating are used to enhance the product’s aesthetics and protect it from corrosion. The choice of finishing technique depends on the product’s function, the environment it will be used in, and the desired aesthetic appeal.
How to Choose Sheet Metal Fabrication Services
When choosing a fabrication service, consider factors like the company’s experience, the range of services offered, their technological capabilities, and their track record of delivering quality products on time
Conclusion
The world of sheet metal fabricators is a testament to the perfect blend of art and science, showcasing human ingenuity at its best. As technology continues to advance, the scope and capabilities of these fabricators will only expand, underlining their critical role in our modern society. Whether it’s a custom, one-off piece or mass-produced components, the intricate process of sheet metal fabrication continues to shape our world, one sheet at a time.