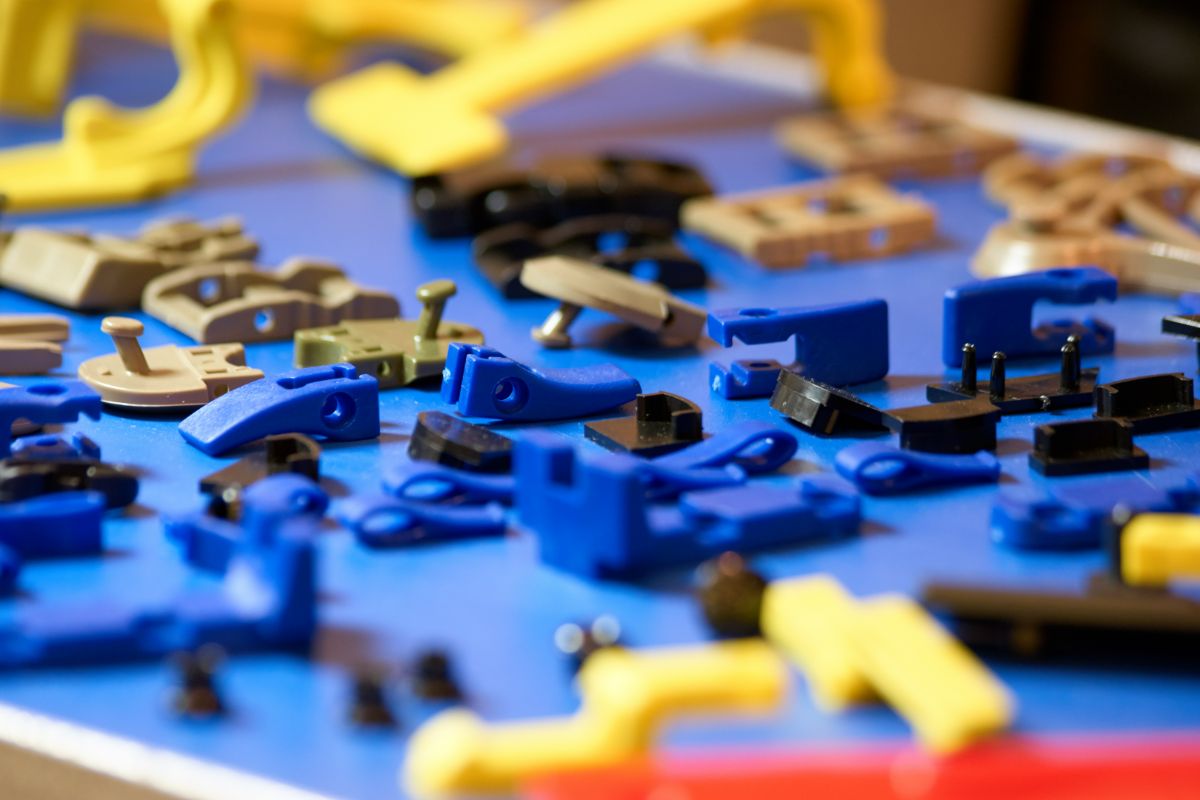
In the world of manufacturing and plastic production, the choice between precision plastic injection molding and conventional molding can be a critical decision that impacts product quality, cost-effectiveness, and overall efficiency. While both techniques play pivotal roles in shaping plastic components, they are distinct in their methodologies and advantages.
This article delves into the fascinating realm of plastic molding processes, unraveling the differences that set precision plastic injection molding and conventional molding apart. By the end of this exploration, you’ll gain a deeper understanding of which method might be the best fit for your specific production needs and why precision matters in today’s competitive manufacturing landscape. Join us as we journey into the heart of these molding processes to unveil the secrets that make them unique and valuable in their own right. Read on.
Tolerance and Precision
When it comes to tolerance and precision, precision plastic injection molding and conventional molding stand apart in notable ways. Precision plastic injection molding shines in its ability to achieve incredibly tight tolerances, often in the micron range. This method leverages advanced machinery, computer-aided design (CAD) systems, and precise control over variables like temperature and pressure to consistently produce highly accurate and uniform plastic parts. In contrast, conventional molding, while effective for many applications, typically offers slightly lower precision due to variations in factors like material flow and cooling rates.
The key takeaway here is that if your project demands exceptional precision and tight tolerances, precision plastic injection molding is the superior choice, ensuring consistent and exacting results for your components.
Complexity of Parts
As you consider the complexity of parts, precision plastic injection molding and conventional molding exhibit distinctive characteristics. Precision plastic injection molding excels when it comes to intricate and complex part geometries. Its precise control over material flow, along with the ability to create multi-cavity molds, makes it ideal for producing intricate components with tight features. This method is favored for projects that involve complex shapes, fine details, or components with varying wall thicknesses. Conventional molding, on the other hand, is better suited for simpler, less complex parts where precision and intricate designs are not the primary focus.
If your project involves intricate and detailed components, precision plastic injection molding offers the superior capability to meet these demands efficiently and consistently.
Materials and Materials Handling
Precision plastic injection molding is highly versatile and compatible with a broad range of materials, including thermoplastics, thermosetting plastics, elastomers, and even certain metal powders in advanced applications. The precise control over material flow and temperature allows for the use of specialized materials with ease. Additionally, precision molding often involves meticulous materials handling, ensuring the purity and consistency of the material throughout the process.
Conversely, conventional molding is generally more limited in terms of materials. It’s commonly used for thermoplastics and some basic thermosetting plastics but may struggle with more exotic or advanced materials. Materials handling in conventional molding is often less precise due to the simpler machinery used.
Therefore, if your project requires a broader material selection or demands strict control over material quality and consistency, precision plastic injection molding emerges as the preferred choice, offering a wider range of possibilities and the necessary precision in handling materials.
Tooling
In terms of tooling, precision plastic injection molding and conventional molding exhibit notable distinctions. For one, precision plastic injection molding typically requires more intricate and customized tooling. The molds used are precision-engineered to exact specifications, allowing for complex shapes and tight tolerances. These molds can be expensive and time-consuming to create but offer unmatched precision and repeatability.
With conventional molding, it often employs simpler, less customized molds, making it more cost-effective for basic shapes and larger production runs. The tooling for conventional molding is typically quicker and more affordable to produce but may not accommodate the same level of complexity or precision as precision plastic injection molding.
The choice between these methods often hinges on the intricacy and precision required for your specific project, with precision plastic injection molding offering superior tooling capabilities for intricate, high-precision components.
Production Volume
Precision plastic injection and conventional molding also pose significant differences in terms of manufacturing processes. For instance, precision plastic injection molding is exceptionally well-suited for both low and high production volumes. Its ability to produce consistent, high-precision parts efficiently makes it a preferred choice for small to large production runs. Additionally, the use of multi-cavity molds allows for simultaneous production of multiple parts, further increasing output rates.
Conventional molding, while cost-effective for high-volume production, can face limitations with smaller runs due to the setup time and tooling costs involved.
Therefore, when considering production volume, precision plastic injection molding offers the flexibility to cater to a wide range of project sizes, making it a versatile choice for manufacturers with varying production needs.
Key Takeaway
The distinctions between precision plastic injection molding and conventional molding are profound and pivotal when it comes to selecting the right manufacturing process for a specific project. Precision plastic injection molding stands out for its unmatched precision, intricate part capabilities, and compatibility with a broad range of materials, making it the ideal choice for complex, high-precision components. It excels in both low and high production volumes, offering flexibility and consistency. In contrast, conventional molding, while cost-effective for large-scale production, may be limited in terms of precision, materials, and intricate part designs.
The choice between these methods hinges on the unique requirements of each project, highlighting the importance of selecting the right molding process to ensure the highest quality and efficiency in plastic component production.